
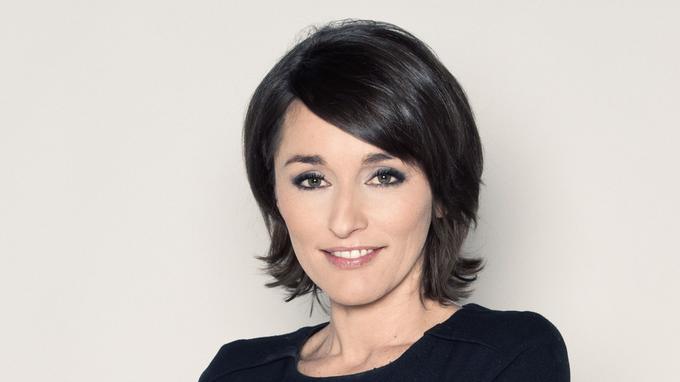
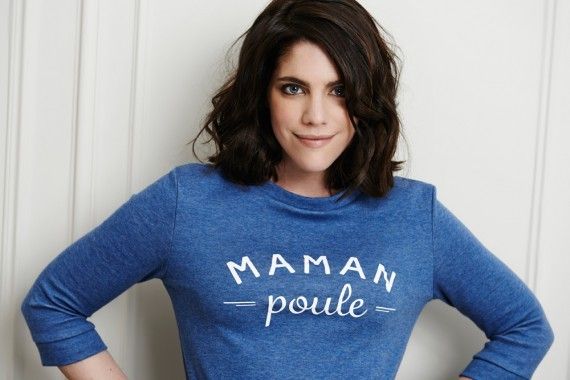
These attributional coproduct allocation schemes are shown conceptually in Fig. 1.Īttributional life-cycle inventories (LCI) have been widely used in life-cycle assessments (LCAs) of commodity chemical products such as polyethylene, polypropylene, polyethyleneterephthalate, and polystyrene ( Liptow and Tillman, 2012 Harding et al., 2007 Tabone et al., 2010). In a displacement method, the energy, raw materials, wastes, and emissions attributed to ethylene, in a process producing ethylene and coproducts, would be calculated by subtracting the inventory elements required to separately produce the coproducts from the total process energy, raw materials, wastes, and emissions. Displacement methods are also used in coproduct allocation. So, for example, if ethylene production yields the primary product ethylene, along with coproducts of propylene, butylenes, and butadiene, then the energy and raw material use in the manufacturing process would be attributed to the ethylene, propylene, butylenes, and butadiene, based on the energy content of the products, the mass of the products, or the value of the products. Often in the chemical manufacturing of products such as ethylene, coproducts will be generated, and in an ALCI, material use, energy use, wastes, and emissions are attributed to the primary product and coproducts based on various allocation or displacement rules. The next steps in the sequence involve manufacturing ethylene and polyethylene from the petroleum and NGLs. For example, in the manufacture of polyethylene, the raw material extraction steps yield petroleum and natural gas liquid (NGL) (ethane, propane, and other light alkanes) products. Attributional LCIs (ALCIs) track material use, energy use, coproduct generation, wastes, and emissions through sequential processing steps, encompassing raw material extraction, refining and processing, product manufacturing, product use, and recycle or disposal. Life-cycle inventories (LCIs) can be broadly classified as attributional and consequential.
Animatrice lci iso#
Some of the well-known and accepted methodologies are, among others, ISO 14040, UNEP/SETAC, and International Life Cycle Data System (ILCD) ( Azapagic, 1999). The damage-oriented methods also separate the flows into environmental burden classes but take it further by modeling and cataloging their effects according to the effect on human health, ecosystem, and resources ( Azapagic, 1999). The problem-oriented methods aim to simplify a very complex set of data, dividing the flows into a few environmental burden classes ( Azapagic, 1999). One of two methods is followed: problem-oriented methods (midpoint) and damage-oriented methods (endpoint). With respect to LCIA, it converts the inventory into simple indicators. What share of the environmental burdens should be allocated to the product in question, i.e., in the LCI? Different solutions have been proposed, with the most well known being ISO 14041 ( Vanegas, 2003). When producing more than one product, an allocation problem rises. LCI quantifies the inputs and outputs of a system, material, and energy flows. LCA is commonly divided into four distinct parts: goal and scope definition LCI life cycle impact assessment (LCIA) and interpretation. Rafiqul Gani, in Assessing and Measuring Environmental Impact and Sustainability, 2015 LCA: methodologies
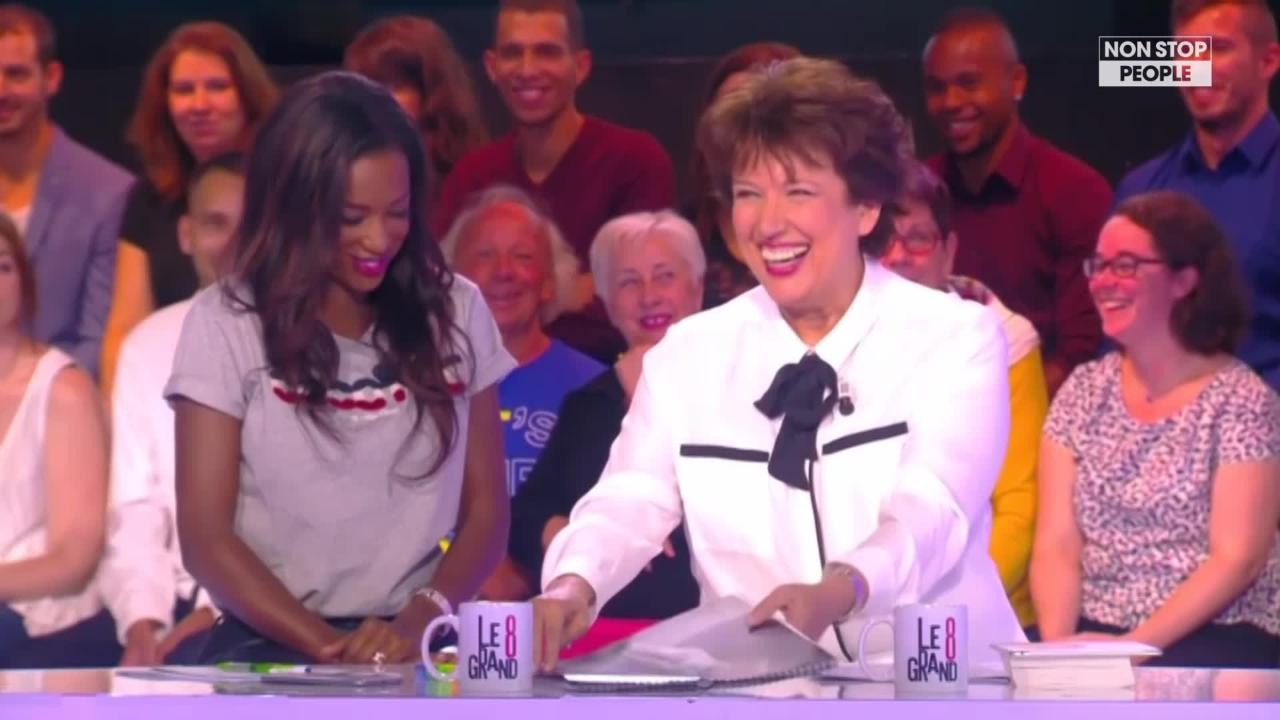
Methods and tools for sustainable chemical process designĬarina L. Figure 2 shows a very good match between LCSoft and SimaPro7.1. The comparison results are shown in figure 2 where the horizontal axis indicate different elementary flow (energy and substance flow) considered and the vertical axis represents the ratio of LCI results from LCSoft to SimaPro7.1. Acetic acid, 98% in H2O, at plant - RER from ecoinvent data v2.0 ( Althaus et al., 2007) is taken to calculate LCI with LCSoft and SimaPro7.1 from cradle to gate and LCI calculation model in LCSoft is validated by comparing LCI results with SimaPro7.1. “B” represents the intervention matrix that contains pollutants, natural resources, or energy emitted or consumed by processes, while, “s” is a scaling factor that is used to scale up unit processes in the technology matrix to the achieve target value defined by a functional unit. Inflow and outflow are noted by positive and negative values, respectively. In Table 2, “A” represents the technology matrix that contains commodity flow of all processes. Life Cycle Inventory calculation is developed for compiling and quantifying all elementary flow through the related process based on the model given in Table 2.
